Motor rewinding is a process of repairing and refurbishing an electric motor by rewinding the stator or rotor windings, which are the electrical circuits that carry the current to produce the magnetic field. This process is typically performed when the motor has failed due to worn-out or damaged windings, overheating, or other electrical issues.
The motor rewinding process involves several steps:
- Disassembly: The motor is disassembled to access the stator or rotor windings.
- Inspection: The windings are inspected to identify the extent of the damage and determine the necessary repairs.
- Cleaning: The windings are cleaned to remove dirt, debris, and old insulation.
- Rewinding: New wire is wound onto the stator or rotor core to replace the damaged or worn-out windings.
- Insulation: New insulation is applied to the windings to prevent electrical shorts and ensure proper operation.
- Reassembly: The motor is reassembled, and the windings are connected to the electrical terminals.
- Testing: The motor is tested to ensure it is operating within the specified parameters and performance standards.
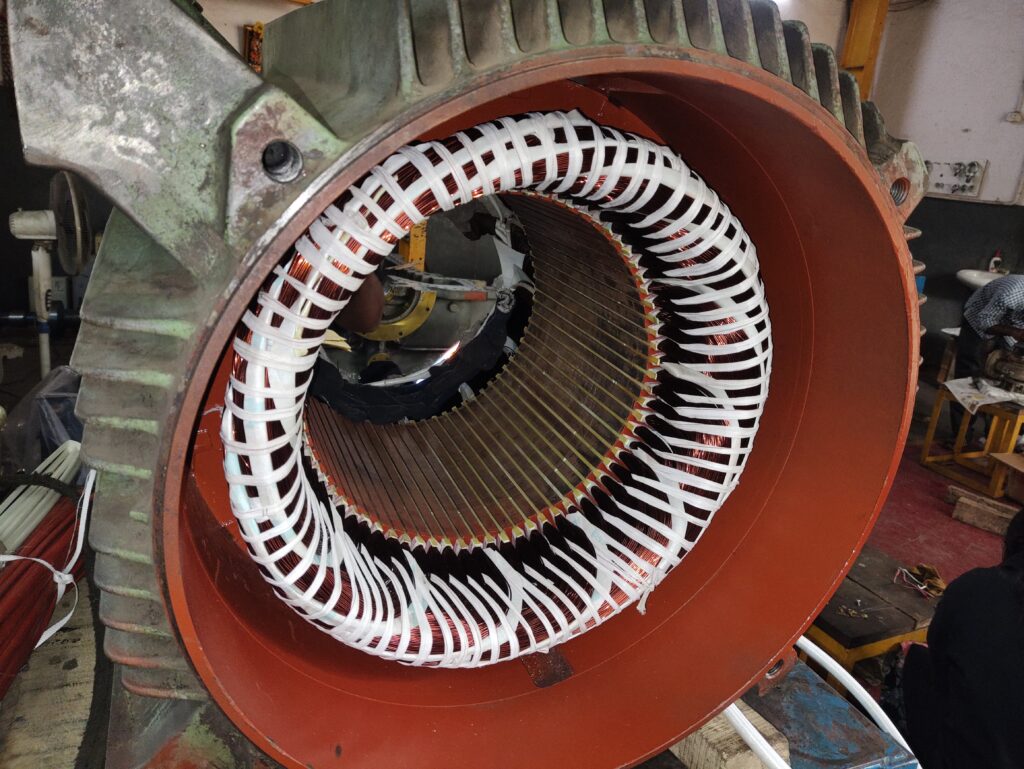
Motor rewinding can be a cost-effective and environmentally friendly option compared to replacing the entire motor. It can also help to extend the lifespan of the motor and reduce downtime. However, it is essential to note that not all motors can be rewound, and the decision to rewind or replace a motor depends on various factors, including the motor’s age, condition, and application.
In the context of industrial maintenance, motor rewinding is a critical service that can help to minimize downtime, reduce energy consumption, and improve overall equipment efficiency. It is often performed by specialized technicians or companies that have the necessary expertise and equipment to perform the rewinding process correctly and safely.